電液伺服技術(shù)在蝶閥上的應(yīng)用
將電液伺服技術(shù)應(yīng)用于蝶閥蝶板的高精度控制,給出高精度電液伺服控制蝶閥的結(jié)構(gòu),利用AMESim軟件建立仿真模型,探討各主要結(jié)構(gòu)參數(shù)對其動靜態(tài)特性的影響,并進行動靜態(tài)試驗。理論分析和試驗結(jié)果表明:電液伺服控制蝶閥精度高、線性度好、滯回小、頻響可根據(jù)工程實際進行設(shè)定,調(diào)整方便。目前,該蝶閥已在工程中應(yīng)用。除蝶閥外,電液伺服技術(shù)也可用于球閥等閥門的高精度流量控制。
蝶閥由于其結(jié)構(gòu)緊湊、啟閉迅速、流阻小、流量系數(shù)大,容易實現(xiàn)大口徑、大流量的流體輸送等特點,廣泛應(yīng)用于煉鋼、電力、水利、化工等領(lǐng)域。目前,蝶閥主要應(yīng)用于啟閉控制,隨著生產(chǎn)過程精度控制要求越來越高,還要求通過控制蝶閥蝶板的轉(zhuǎn)動角度來控制輸送的流量。隨著計算機技術(shù)的發(fā)展和電液伺服技術(shù)的廣泛應(yīng)用,高精度流量控制的蝶閥成為一種可能。
基于電液伺服技術(shù)響應(yīng)快、精度高、體積小、輸出力矩大等特點,作者提出了一種電液伺服控制蝶閥的結(jié)構(gòu),并根據(jù)其結(jié)構(gòu)建立了AMESim仿真模型,對其動靜態(tài)特性進行仿真分析,探討系統(tǒng)各主要參數(shù)對動靜態(tài)特性的影響,并進行試驗驗證。
1、工作原理
圖1為電液伺服控制蝶閥系統(tǒng)結(jié)構(gòu)圖,考慮到蝶閥控制所需油液很少,不必單獨增設(shè)液壓源,壓力油可直接從主液壓系統(tǒng)引入,并利用單向閥、蓄能器、減壓閥等元件,可減少主液壓系統(tǒng)壓力波動對電液伺服控制蝶閥系統(tǒng)的性能影響。主系統(tǒng)油泵9經(jīng)減壓閥7將液壓油減壓輸送至伺服閥5,在輸入信號作用下,伺服閥5的閥芯移動,高壓油進入液壓缸4的一端,另一端通過伺服閥接回油,在壓差的作用下,使液壓缸活塞運動,并通過銷與撥叉3,驅(qū)動蝶閥閥桿轉(zhuǎn)動,使蝶板2轉(zhuǎn)動。蝶板的轉(zhuǎn)角由角度傳感器1檢測并反饋回輸入端,與輸入信號相比較得出誤差信號,經(jīng)放大器放大后輸入伺服閥5,使蝶板的轉(zhuǎn)動角度與輸入角度相吻合。
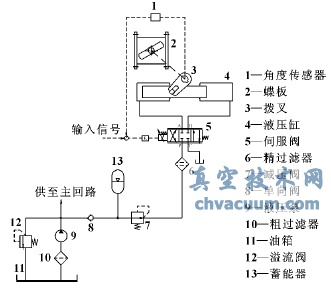
圖1 電液伺服控制蝶閥系統(tǒng)結(jié)構(gòu)圖
2、建模與分析
為了更準確地反映系統(tǒng)的運動規(guī)律,利用AMESim軟件,建立了如圖2所示的液壓系統(tǒng)仿真模型。
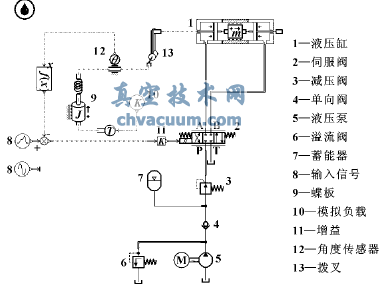
圖2 仿真模型
當對仿真模型輸入階躍信號時,角度傳感器的輸出響應(yīng)曲線如圖3所示?梢姡寒旊A躍信號為4~20mA時,蝶閥蝶板實現(xiàn)了0°~90°的轉(zhuǎn)動,開啟響應(yīng)時間約0.92s,關(guān)閉響應(yīng)時間約0.97s。
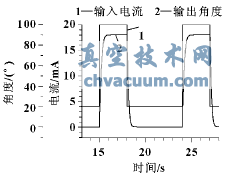
圖3 階躍特性的仿真曲線
3、仿真分析
系統(tǒng)的主要仿真參數(shù)有:減壓閥調(diào)定壓力、系統(tǒng)壓力、增益K、液壓缸活塞油壓作用面積、模擬負載扭矩等;诮⒌姆抡婺P,探討各主要參數(shù)對動態(tài)特性的影響,從而進行優(yōu)化設(shè)計。改變上述參數(shù),對動態(tài)特性進行仿真分析,仿真結(jié)果表明:
(1)如圖4所示,隨著減壓閥3調(diào)定壓力的增大,階躍響應(yīng)時間逐漸縮短。當減壓閥調(diào)定壓力過低時,系統(tǒng)無法將蝶閥開啟;而當減壓閥調(diào)定壓力過高時,蝶板則轉(zhuǎn)動太快。因此,應(yīng)根據(jù)應(yīng)用場合選擇合適的減壓閥調(diào)定壓力,該系統(tǒng)減壓閥調(diào)定壓力范圍為6~15MPa。
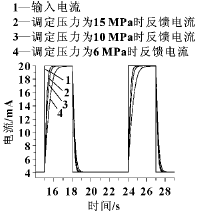
圖4 減壓閥調(diào)定壓力的影響
(2)通過調(diào)整仿真模型中溢流閥6的壓力,模擬主系統(tǒng)油源壓力波動,系統(tǒng)壓力對響應(yīng)的影響如圖5所示?梢姡3條反饋電流信號曲線基本重合,即由于系統(tǒng)采用了單向閥、蓄能器、減壓閥等元件,使減壓閥出口壓力保持不變,蝶板的角度控制特性不受系統(tǒng)壓力變化的影響。
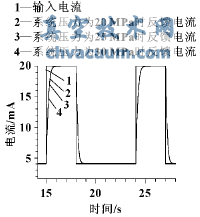
圖5 系統(tǒng)壓力的影響
(3)如圖6所示,蝶板轉(zhuǎn)動的階躍響應(yīng)時間隨放大器增益K的增大而縮短。K值太小,響應(yīng)過慢;而K值太大,則蝶板轉(zhuǎn)動太快。當減壓閥調(diào)定壓力為15MPa時,增益K取0.8~3,開啟響應(yīng)時間約1.27~0.51s,關(guān)閉響應(yīng)時間約1.12~0.49s。
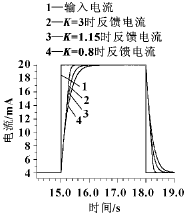
圖6 增益的影響
(4)液壓缸活塞油壓作用面積對蝶板響應(yīng)特性的影響如圖7所示?梢姡呵2的作用面積過小,產(chǎn)生的力不足以推動閥門啟閉,而曲線4的作用面積過大,在流量相同的情況下,運動速度相對較慢,響應(yīng)時間較長。因此,該系統(tǒng)中選用活塞直徑40mm。

圖7 液壓缸活塞油壓作用面積的影響
(5)如圖8所示,隨著模擬負載扭矩的增大,階躍響應(yīng)速度減慢,當負載扭矩增大到一定值后,蝶板將無法開啟。該系統(tǒng)中模擬負載扭矩取200N·m。
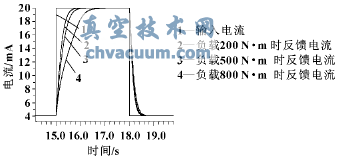
圖8 模擬負載的影響
4、試驗分析
在上述仿真分析的基礎(chǔ)上,搭建試驗系統(tǒng)對電液伺服控制蝶閥液壓系統(tǒng)進行了動靜態(tài)試驗驗證。試驗系統(tǒng)原理如圖9所示,信號發(fā)生器發(fā)送階躍或正弦信號,經(jīng)直流電源偏置后,由采樣電阻采樣并輸送至示波器讀出;驅(qū)動電流與反饋電流比較后,經(jīng)伺服放大器放大輸入伺服閥;伺服閥驅(qū)動液壓缸使撥叉轉(zhuǎn)動,撥叉帶動蝶閥蝶板轉(zhuǎn)動,轉(zhuǎn)動角度由角度傳感器測量并反饋,經(jīng)采樣電阻采樣后由示波器讀出。
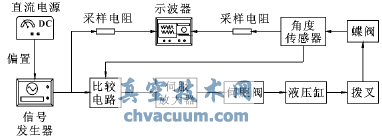
圖9 試驗系統(tǒng)原理圖
減壓閥調(diào)定壓力為15MPa時的電流—蝶板轉(zhuǎn)角靜態(tài)特性試驗與仿真曲線如圖10所示。3條曲線(仿真曲線、蝶板轉(zhuǎn)角上升曲線、蝶板轉(zhuǎn)角下降曲線)基本重合,說明蝶閥蝶板的轉(zhuǎn)動與驅(qū)動電流呈良好的線性關(guān)系,且滯回很小,并驗證了仿真模型。
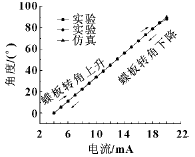
圖10 靜態(tài)特性的試驗與仿真曲線
圖11所示為減壓閥設(shè)定壓力為15MPa時,示波器記錄的階躍響應(yīng)曲線。可見,蝶閥蝶板開啟時間為1s,關(guān)閉時間為1.2s。
減壓閥設(shè)定壓力為15MPa時,蝶閥蝶板轉(zhuǎn)動頻響試驗結(jié)果為0.94Hz(頻響的仿真結(jié)果為0.95Hz),如圖12所示,試驗結(jié)果與仿真結(jié)果基本吻合。
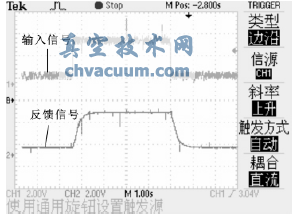
圖11 階躍特性的試驗曲線
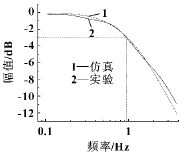
圖12 幅頻特性的試驗與仿真曲線
5、結(jié)束語
理論分析與試驗結(jié)果表明:將電液伺服技術(shù)應(yīng)用于蝶閥流量高精度控制是可行的。除蝶閥外,也可應(yīng)用于球閥等閥門。目前,該蝶閥已成功應(yīng)用于鋼廠熱軋系統(tǒng)中。