采用稀土共滲技術解決汽車齒輪滲碳存在的問題
當前我國汽車齒輪仍然存在著滲碳溫度高,工藝周期長,齒輪變形大,使用壽命短,質量欠佳,能耗過高等問題。用什么方法可以解決上述長期存在的老大難問題,是擺在我國科技與工程工作者面前的嚴峻任務。經過長期的研究與生產實踐,我們提出采用稀土共滲技術可以多方面、完滿地解決上述難題。使我國齒輪滲碳技術上一個新臺階,產品質量達到或超過國際標準。
我國自進入WTO以來,汽車市場逐步對外開放,國外一些知名汽車制造商紛紛在中國設廠,引進了大量先進制造沒備與先進工藝技術,預計今年全年各類汽車生產將突破400萬輛大關,對我國汽車行業(yè)帶來巨大沖擊與發(fā)展機遇,競爭將越來越激烈j隨著汽車市場全球化趨勢的發(fā)展,中國必將成為全球汽車零配件制造與供應商主要集貿市場。要想抓住這個商機,必需按國際標準進行生產。汽車齒輪及其總成是汽車極其重要的零部件,如能克服上述存在問題(見摘要),使之成為名牌產品,其變速箱與后橋成為世界知名品牌汽車的直接供貨商,參與世界市場競爭并贏得市場份額,將為我國汽車制造業(yè)做出重大貢獻。
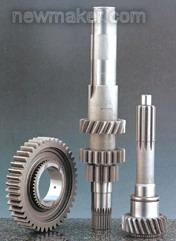
稀土共滲技術是哈爾濱工業(yè)大學20世紀80年代中期重大的科技發(fā)明。學者們首先發(fā)現(xiàn)能將原子半徑比鐵大40%的稀土原子滲透人到了鋼的表而,同時發(fā)現(xiàn)稀土對滲碳、碳氮共滲、滲氮等化學熱處理過程有十分明顯的催滲作用,可以提高滲速20%~30%。理論研究指出,微量的稀土(數十個ppm)滲人到鋼的表層后還能起微合金化作用,它能有效地成為第二相如碳化物、碳氮化合物或氮化物,沉淀析出的核心,進而沉淀析出細小彌散顆粒狀碳化物與碳氮化物。這些高度彌散的顆粒必將成為奧氏體向馬氏體切變長大的障礙物,迫使馬氏體轉變?yōu)槌毣。這種超細馬氏體具有很高的強度與韌性,作為基體其上分布細小彌散顆粒狀碳化物,這就是稀土共滲后獲得的最佳微觀組織,這種最佳組織具有更高的接觸疲勞與彎曲疲勞強度以及足夠高的硬度與耐磨性和抗粘著磨損特性。由上述可見,在齒輪滲碳中正確引入稀土碳共滲技術不僅可提高滲速20%~30%,還能獲得其他方法難以得到的最件金相組織,由此帶來使用性能的大幅攀升。
由于滲劑中加入稀土既能提高滲速降低能耗,減少變形,又能明顯改善組織和提高性能,因此如在齒輪滲碳中引入稀上將使我國化學熱處理工藝提高至一個新水平,產品質量上一個新臺階,從而早日完成與國際接軌的目標,參與國際競爭。
一、當前汽車齒輪滲碳存在的問題與差距
1.普遍存在的問題
(1)滲碳速度慢,生產效率低,能耗居高不下。
(2)滲碳溫度高,碳勢Cp高,導致金相組織差,碳化物、馬氏體、殘留奧氏體等級別偏高,且級別波動大,穩(wěn)定性差。
(3)齒輪經熱處理后尺寸畸變大,精度等級大幅下降,裝配互換性變差,傳動欠平穩(wěn)、噪聲大。
(4)性能差 ①表面存在黑色組織與非馬氏體組織。②外表層殘留奧氏體過多。③外表層硬度偏低,硬度分布曲線表面層低頭現(xiàn)象普遍,導致耐磨性大幅下降,④齒輪接觸疲勞性與耐磨性不高,導致齒面出現(xiàn)麻點剝落,造成早期疲勞失效損壞,這點在載重車與重型工程車輛中表現(xiàn)尤為突出。
2.與國際接軌配套出口存在差距
前已述及我國生產汽車產量已躍居世界第三,汽車生產基本上為外商壟斷,我國汽車工業(yè)的出路在于提供大量優(yōu)質零配件。以齒輪為主的汽車傳動系統(tǒng)對汽車來說極為重要,以齒輪為主組成的汽車發(fā)動機變速箱總成與前橋和后橋總成若能與世界汽車制造商提供配套,將是我國汽車行業(yè)一個重大機遇。為此,齒輪行業(yè)尤其是齒輪熱處理行業(yè)應認清形勢,為達到出口水平而做出應有的努力。
總的說來,達到出口配套必須在加工流程中對如下環(huán)節(jié)加強工藝控制,否則必然產生差距。
(1)熱處理前的機加工質量包括:表面粗糙度與尺寸公差,即熱處理前后的外觀質量與裝配精度。
(2)與性能及尺寸變形相關的材料與加工工藝,包括:鋼材成分控制與純凈度、淬透性帶控制、帶狀組織控制、鍛坯的預先熱處理等溫正火及組織的均勻性,冷加工應力消除等。
(3)滲碳淬火回火過程齒輪的畸變控制與精度等級控制,裝配互換性、傳動平穩(wěn)性與噪聲。
(4)工裝設備方面,氧化脫碳、工件表面清理、淬火油冷卻特性與冷卻均勻性(包括工件料筐擺放)等。
(5)金相組織差異:表面硬度與硬度梯度分布,碳化物、馬氏體與殘留奧氏體級別控制。
(6)性能抽檢:①齒輪彎曲疲勞與接觸疲勞試驗。②變速箱與后橋總成臺架壽命試驗等。
外商通常對齒輪產品進行如下檢驗:
(1)齒輪外觀檢查:①商品色澤。②公差尺寸檢查。③表面粗糙度。
(2)裝配互換性檢查:總成傳動振動與平穩(wěn)性榆查,總成傳動噪聲檢查。
(3)熱處理質量檢查:①表面硬度62~64HRC。②層深檢查按550HV評定。③金相組織:一般碳化物、馬氏體及殘留奧氏體<3級;嚴格時≤2級。
(4)對加工產品單位質量保證體系考查:①硬件設備:溫度自控智能儀表與校正體系;氧探頭及其智能儀表控制體系;金相質量檢測體系。②軟件:質量管理各種文件與措施;工藝管理各種文件齊全。
只有硬件與軟件達到要求后才可以進行產品加工,目的在于保證產品質量的穩(wěn)定性、可靠性與重復性及均一性。
綜上所述,我國許多企業(yè)經過近10年來的不斷改造,有相當部分企業(yè)的冷熱加工的工裝設備已基本上符合國際生產水平的要求,關鍵問題在于企業(yè)領導者與經營管理者的理念:一是受多年來國有企業(yè)經營管理理念束縛,重產量輕質量,當產生矛盾時往往質量為產量讓路。二是只重視眼前利益,輕視長遠利益。三是缺乏市場競爭意識,缺乏優(yōu)患意識,缺乏創(chuàng)新意識,缺乏企業(yè)生產經營的個性與特性的發(fā)展戰(zhàn)略,沒有個性與特性的企業(yè)只能隨著市場大起大落。因此如何實現(xiàn)思想轉軌及經營管理理念轉軌,加快企業(yè)適應市場特別是汽車市場的全球化的競爭與機遇,在全球“中國造”的大旗下,占領一席之地,有關部門應當認真加以思考。
3.當前重點應急措施——采用稀土碳共滲技術
從技術角度而言,優(yōu)質齒輪的生產是一個系統(tǒng)工程,生產流程各生產環(huán)節(jié)都存在各式各樣的矛盾與問題。實踐證明:齒輪質量的焦點集中表現(xiàn)在熱處理后。
簡言之,—股滲碳淬火后齒輪的精度由熱處理前的4~5級精度,處坪后增至7~8級,尺寸與形狀畸變急劇增大,齒輪裝配的互換性變差,花鍵孔變形導致齒輪中心距偏移,傳動過程產生振動和噪聲將不可避免地增大,后果是汽車變速箱裝配后肯定達不到標準;而齒輪的內在質量更是決定于齒輪熱處理質量,例如行業(yè)規(guī)定,表面硬度58~62HRC,若表面存在黑色組織與非馬氏體組織,勢必影響齒面的承載能力、耐磨性及接觸疲勞壽命,造成早期疲勞磨損而失效。齒向差的變形造成齒而受力偏載也可造成早期失效損壞。特別典型的載重車后橋終端傳動螺旋錐齒傳動付,當轉彎或道路崎嶇不平時,承受巨大沖擊及滑動摩擦,極易產生沖擊疲勞磨損與粘著磨損,這些問題導致集中暴露在熱處理質量上,多年來一直是熱處理的老大難問題,成為我國汽車生產質量的攔路虎與瓶頸。
有沒有辦法解決?有——采用稀土碳共滲技術可以收到立竿見影的實效。
稀土化學熱處理共滲技術是20世紀80年代中期哈工大在材料科學領域中的一項重大科技發(fā)明,首次發(fā)現(xiàn)了稀土滲碳過程中的催滲作用與微合金化作用,先后申請相關發(fā)明專利8項,并獲航天部科技成果一等獎一項“稀土對碳氮共滲過程的活化催滲及其在汽車拖拉機齒輪上的應用”(1986年);國家發(fā)明二等獎“稀土特殊共滲熱處理新技術”(1990年)。
本項技術具有如下獨特的特性:
(1)在滲碳過程中提高滲速15%~30%,下限為嚴格對比,上限包括工藝參數優(yōu)化;對氮化及軟氮化提高30%~50%。
(2)可降低滲碳溫度40~60℃,可在820~900℃溫度下進行快速滲碳,完全取代碳氮共滲消除黑色組織及非馬氏體組織,使工件變形的畸變大幅下降。
(3)改善組織,提高性能。稀土能與碳一起滲入到鋼的表面層起微合金化作廂,稀土能作為碳化物形核核心,使其成為細小彌散顆粒狀沉淀析出。它的存在阻礙馬氏體切變長大,馬氏體殘留奧氏體成超細狀態(tài),所以稀土滲碳的過共析區(qū)的典型組織為:在超細隱晶馬氏體與殘留奧氏體的基體上分布著不同大小尺寸的細小彌散顆粒狀碳化物。這種超細馬氏體與殘留奧氏體具有高強度、高韌性及高的斷裂韌度,高的耐磨性與動態(tài)彎曲疲勞與接觸疲勞壽命。
(4)提高生產效率及勞動生產率,明顯降低能耗,從而降低生產成本。
二、各種催滲劑的簡單比較及新技術應用前景
我國存化學熱處理技術市場上先后出現(xiàn)過如下一些催滲技術及新技術,可簡單分類如下:
1.化學催滲類
(1)四氯化碳及氯離子類、酸性氣體類:機理是利用氯離子在氣相反應中對工件表面反應,清除表面污物,露出新鮮表面,活化工件表面,促進表面反應能力,對滲C、滲N有明顯的催滲作用,作用機理只限爐氣與工件界而反應,除對工件表而產生化學反應外,對爐子耐熱鋼構件有明顯腐蝕作用。
(2)BH催滲技術:強化滲碳劑裂化反應,既使煤油也可在860~880℃低溫裂解,機理為4價碳離子催滲;即使4價碳原子滲入也不會產生合金化作用。
(3)稀土共滲技術:除催滲節(jié)能提高效率外,最大特征與區(qū)別是稀土能滲入鋼的表面層內起微合金化作用,細化組織與提高性能,這是本技術與其他催滲技術的本質差別。
(4)多元共滲:C、N、B、S、O、RE,盡管各個元素起的作用不同,但是稀土RE起第二相沉淀析出核心,細化第二相使之細小彌散分布,不易團聚長大的特殊作用不可能被取代,因此提高工藝溫度,進一步提高滲速及保持高性能的特殊作用十分明顯。
2.物理催滲先進技術
諸如離子氮化、離子軟氮化、離子滲碳、電場滲碳及真空滲碳等,只是處理特殊零什時使用。對汽車齒輪來說,要求批量大、成本低、質量穩(wěn)定,特殊方法難以滿足。故目前仍然沿用常規(guī)設備,如井式滲碳爐、密封箱式滲碳爐及連續(xù)式氣體滲碳爐,只不過進行了必要技術改造,特別是增加了先進的計算機控制系統(tǒng).廣泛采用國際上通用的氧探頭及碳勢控制智能儀表及其上位機——工業(yè)控制計算機及相應的自適應滲碳軟件,這些裝備國內已能自行制造,性能與國外產品基本相同,價格則低很多。
3.與國際接軌及齒輪產品出口配套的技術措施
(1)硬件設備條件 我國熱處理專業(yè)化水平還很低,企業(yè)分散,尚處于轉軌階段,大多數企業(yè)熱處理設備落后,對于質量控制設備,有的不具備或只有一部分,要徹底改變這種現(xiàn)狀只有走專業(yè)化道路。目前只能面對這種現(xiàn)實加強設備、工藝及質量管理,力求最好效果。
(2)工藝軟件及質量管理 采用我國獨創(chuàng)的稀土碳共滲技術,允分發(fā)揮其獨特的作用,加強工藝管理,可使汽車齒輪的滲碳工藝水平達到新水平,產品質量上一個新臺階,生產條件好的企業(yè)達到出口水平完全可能。實踐證明,少量企業(yè)走在前面已成功向外商汽車企業(yè)提供了配套齒輪產品及汽車零配件總成。
三、稀土共滲技術的正確應用
1.稀土滲劑的選擇
為了適應當前市場需求,推進先進工藝技術的應用,推薦稀土共滲技術,我們目前與原哈爾濱稀土材料廠的工程技術人員共同組建了哈爾濱意鋒稀土應用技術開發(fā)公司,業(yè)已研制成功并推出有機稀土共滲催滲劑系列產品。它除了效果優(yōu)良外,還克服了管口堵塞問題,在井式滲碳爐中連續(xù)使用50余爐沒有發(fā)生一次堵塞現(xiàn)象,給用戶使用帶來方便,滿足了市場需求。
2.稀土催滲效果評價
(1)評價內容 催滲含義主要指滲入速度及節(jié)電兩個方面。
(2)評價方法對滲速而言有如下幾種對比方法,即加稀土與不加兩種工藝相比:①不同時間取樣測層深并做出兩條滲碳動力學曲線進行對比。②除去輔助時間之后純滲碳時間的滲碳速度v為總深度δ除以純滲碳時間h,即v=δ/h(mm/h)。③加稀土與不加稀土兩種工藝隨爐淬火試樣直接對比。④對周期性爐一個周期所需時間或層深進行對比。⑤對連續(xù)爐按推料周期與試塊滲層深度進行對比。
3.稀土滲碳工藝的特殊性
欲使稀土滲入鋼中起微合金化作用即能成為第二相碳化物形核核心進而沉淀析出細小彌散顆粒狀碳化物,阻礙馬氏體轉變時切變長大而成為超細馬氏體,因此,滲碳工藝必須采用高的爐氣碳勢。只有提供足夠多的碳原子即過飽和濃度的碳原子,稀土才能達到形核條件,同時也因此增加基體中的缺陷密度,促進碳原子在固相中的擴散速度,才能獲得典型的金相組織。通常920~930℃條件下爐氣碳勢必須采用Cp=1.2~1.3,甚至1,4。但不能在高溫下過早析出碳化物。而較低碳勢Cp=1.0~1.1,效果將不明顯。
4.稀土滲碳的微觀組織評價
由于稀土滲碳工藝要求的特殊性,必須采用較高的Cp進行滲碳,因此滲碳外表面過共析區(qū)必須有在常規(guī)×500倍的顯微鏡下可見的細小彌散顆粒狀碳化物,或隱形更細小不可見的彌散碳化物,兩者的基體都是超細隱晶馬氏體與殘留奧氏體,這就是稀土滲碳的典型最佳金相組組織。圖1是20CrMnTiH鋼經900℃×7h稀土滲碳后的典型最佳金相組織圖;圖2是在相同條件下的金相組織,只是Cp較低,碳化物顆粒很細小而已;圖3則為20CrMnTiH鋼無碳化物的金相組織。
如果稀土滲碳工藝參數不當,也可能出現(xiàn)原機械部頒發(fā)的汽車齒輪滲碳金相檢驗標準規(guī)定的有關碳化物、馬氏體及殘留奧氏體各種級別的組織。
四、稀土滲碳工藝的選擇
按目前生產上滲碳齒輪的模數與滲碳層深度可將其按附表所列進行分類,并根據稀土滲碳特點:提高滲速15%~30%,降低滲碳溫度40~60℃,節(jié)能15%~40%,減少變形40%~60%,明顯改善金相組織,大幅提高工件使用性能等,與齒輪的模數及工作條件相結合,進行統(tǒng)一整合,分別采用不同工藝方法進行稀土滲碳,以最終綜合技術經濟指標及有針對性地解決生產問題作為衡量標準,作為選擇稀土滲碳工藝的依據,以獲取最大技術經濟效果。
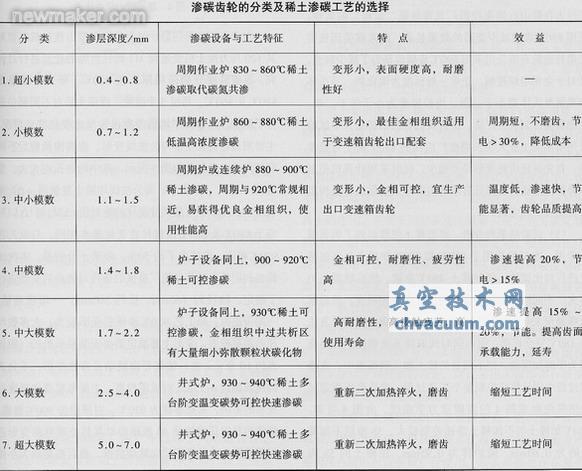
按表中的推薦,結合當前汽車齒輪生產中長期存在的難題,重點推薦及解決汽車變速箱齒輪及載重汽車后橋螺旋盤齒輪傳動的有關稀土滲碳的相關問題。
1.汽車變速箱齒輪傳動副稀土可控滲碳試驗
(1)試驗目的為達到與外資和中外合資汽車制造企業(yè)出口汽車變速箱配套所需齒輪的技術標準而進行試驗,試圖找到解決技術難題的方法與途徑。
(2)試驗設備 105kW的井式及箱式滲碳爐、氧探頭及碳勢控制智能儀表,并應用工業(yè)計算機滲碳軟件進行自動及半自動控制(碳控系統(tǒng)均為北京匯捷通新科技公司提供),進行了50余爐次的試驗。稀土催滲劑由哈爾濱意鋒稀土應用技術開發(fā)公司提供。
(3)試驗材料及齒輪的來源 20CrMnTiH及20CrMoH兩種鋼。試驗齒輪主要為外協(xié)件及哈爾濱傳動箱廠提供的少量試驗齒輪。滲碳層深度要求層深1.1~1.5mm,主要考察齒輪變形、催滲效果及組織控制。
(4)稀土滲碳試驗的工藝設計與外商配套存在的主要問題為:①滲碳淬火后尺寸精度大幅下降,根據我們過去在鞍山紅旗拖拉機廠及青島第二齒輪廠的實踐,采用880℃滲碳減少變形的效果顯著。經考察美國獨資法斯特齒輪有限公司采用890℃滲碳也是為了減少畸變。②對于金相組織控制,企業(yè)一般標準為碳化物、馬氏體和殘留奧氏體要小于三級,內控標準為小于等于二級。金相檢驗控制甚為嚴格。結合我們自己的經驗,本試驗采用哈爾濱工業(yè)大學長期推廣應用的880℃稀土可控滲碳,首先保證齒輪變形盡可能少,同時采用計算機控制碳勢稀土滲碳,既保證有較高的滲速又要保證將金相組織控制在二級之內。
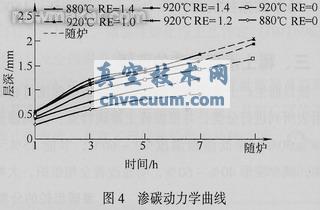
(5)試驗結果和分析新型稀土催滲起到了明顯催滲作用。本試驗采用了880℃和920℃加稀土與不加稀土進行對比試驗。例如稀土880℃滲碳,然后降溫出爐淬火,不同時間取樣測定滲層深度及金相硬度;然后斷電降溫至850℃出爐淬火。920℃稀土滲碳的過程及方法與880℃完全相同,而不同時間取樣方法相同。所用滲劑為甲醇加煤油。把不同量的稀±加入到煤油中,在滲碳過程中用計算機控制整個工藝過程,最后將所測定試驗結果繪制成圖4的滲碳動力學曲線。由圖4可知,880℃加稀土與不加稀土滲速差別較大,5h滲層不加稀土的為O.80mm,隨爐樣為O.95mm,加稀土的5h為1.0mm,隨爐樣達1.2mm,滲速提高25%左右。若與920℃不加稀土的相比,由圖4動力學曲線可知,滲速相比似乎較慢,但對105kW井式爐而言,由880℃升溫至920℃約需20~30min,這與裝爐量有關,而由920℃降至830℃至少需1h,為此達到相似的滲碳層深度兩者的工藝周期,對1.10~1.50mm層深偏下限時880℃所用工藝周期時間反而更短,偏中限時兩者基本相同,節(jié)電可達20%至25%,而變形則大幅下降。對于920℃加稀土與不加稀土相比較而言,不加稀土7h層深為1.4mm,加稀土者達1.7mm,兩者相比提高滲速約21%。
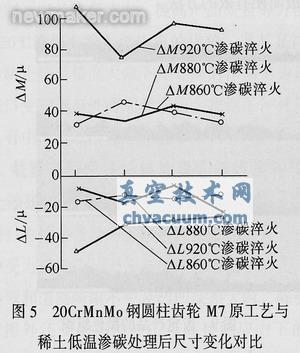
對于齒輪變形問題,過去我們在鞍山拖拉機廠曾對其120馬力推土機變速箱M7圓柱齒輪的變形進行過研究,滲碳溫度分別采用原工藝920℃,稀土滲碳溫度880℃及860℃,每組5個齒輪,滲碳先后對不同部位進行了測量,然后取平均值考察齒輪尺寸變化波動情況,主要測量花鍵孔變形與公法線變形,滲碳淬火前后不同部位尺寸波動變化如圖5所示。其中的內孔均長大,差值用+△M,μ來表示;而公法線均縮小差值用-△L來表示,由圖5中可見尺寸變化的絕對值∣△M∣與∣△L∣對應于880℃及860℃兩組尺寸變化基本相同,與原工藝920℃相比,均減少了約50%,效果十分明顯。本次試驗也利用哈爾濱傳動箱廠提供的條件對軸齒的變形進行了測定,軸徑約如60mm,長約360mm,一端帶花鍵,一端帶錐齒,原工藝920℃滲碳后變形較大,大多數均超差需要校直。變形主要測定需要安裝軸承處的(距錐齒約10余mm處)軸的徑向跳動及彎曲變形,千分表的跳動超過0.15mm時就需校直。主要考察滲碳溫度對變形的影響,常規(guī)滲碳為920℃,對照組為900℃滲碳,滲碳后每組任意選擇40根軸齒對其熱處理彎曲變形進行了檢測,并記錄下徑向跳動數據,最后按跳動大小排列并做成如圖6所示圖形進行比較。若以跳動0.15mm作為變形標準,則原工藝40根中合格18根,約占47%,而對照組900℃滲碳不合格的僅2根,約占5%。可見溫度對變形的影響很大。也就是說降低滲碳溫度是減少變形最有力的措施。
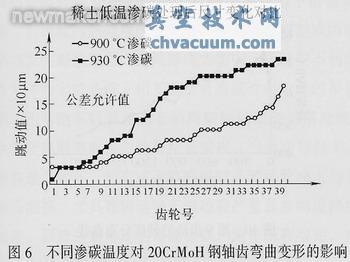
2.應用實例
采用880~900℃加稀土降低滲碳溫度減少齒輪畸變的應用實例如下:
(1)鞍山紅旗拖拉機的100~200馬力推土機變速箱齒輪因滲碳淬火變形大,缺乏互換性,裝配極為困難而成為企業(yè)難題。采用哈爾濱工業(yè)大學的880℃稀土低溫滲碳后徹底解決了這一難題,經檢測,減小變形達50%左右。
(2)吉林一汽輕型車廠早年生產小型面包車時,其后橋螺旋盤先在井式爐中920℃滲碳,然后在箱式爐中重新加熱,在淬火壓床上壓淬,在哈爾濱工業(yè)大學的推薦下,采用860℃稀土滲碳,在改進裝料吊具后實現(xiàn)了滲碳后直淬,取消了壓淬。
(3)青島第二齒輪廠生產中巴以下汽車前后橋總成,其后橋螺旋盤齒如上所述滲碳淬火后二次加熱壓淬,改進掛具后利用多用密封箱式爐采用哈爾濱工業(yè)大學提供的880℃稀土滲碳技術,實現(xiàn)了生產后直淬,取消了壓淬。
(4)一汽變速箱分廠在連續(xù)式滲碳爐中處理同步器帶齒滑套,920℃滲碳后因變形大需在轉底式爐中重新加熱后取出壓淬,在哈爾濱工業(yè)大學幫助下采用900℃稀土滲碳,實現(xiàn)了滲碳后直淬,取消了壓淬。
從以上實踐證明,解決滲碳齒輪的畸變變形,起主要作用的是滲碳溫度,這是主要矛盾的主要方面。降溫滲碳后是否能達到出口產品的尺寸精度標準,還涉及矛盾的次要因素。工程技術界普遍認同如下問題必須嚴格控制:
一是鋼材的冶金質量:淬透性帶帶寬控制;帶狀組織級別控制;夾雜級別控制。
二是鍛坯及預先熱處理:①粗大晶粒的產生及遺傳。②正火組織的不均勻性如局部產生粒狀貝氏體等,由于組織的不均勻性,易造成組織轉變的先后不同而出現(xiàn)局部微區(qū)應力集中導致變形,故德國大眾公司嚴格規(guī)定鍛造毛坯必須嚴格執(zhí)行等溫正火工藝。
三是機加工的加工應力的產生及消除。
四是淬火液冷卻特性及冷卻的均勻性等。
由此可見解決齒輪變形是一個系統(tǒng)工程,但主要矛盾在于材料與熱處理質量,這是不可否認的事實,應面對現(xiàn)實認真對待,找出問題加以解決。
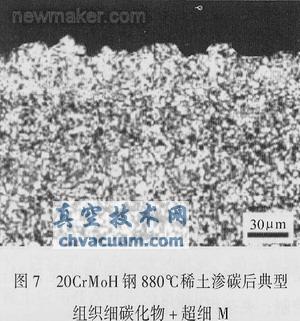
對于金相組織控制,本次試驗推薦的滲碳溫度為880℃,與常規(guī)工藝920~930_℃相比,金相組織相對容易控制。因為溫度低奧氏體晶粒不易長大,即使過共析區(qū)沉淀析出稀土為核心的碳化物,其長大速度很小,也不易成為高級別特征的碳化物。如前所述,欲充分發(fā)揮稀土的作用,必須采用足夠高的碳勢,使之成為碳化物的核心,進而沉淀析出細小彌散的碳化物,促使馬氏體轉變?yōu)槌汃R氏體及殘留奧氏體,從而獲得高硬度與耐磨性、高的沖擊與斷裂韌度及高的彎曲疲勞與接觸疲勞強度。典型的金相組織見圖1、圖2、圖7和圖8。若碳勢控制不當也可能沒有碳化物出現(xiàn),或出現(xiàn)碳化物、馬氏體及殘留奧氏體均為3~4級組織。對有碳控智能儀表及工業(yè)計算機控制的設備,建議采用多段即多臺階碳勢控制,可以收到更好的結果。
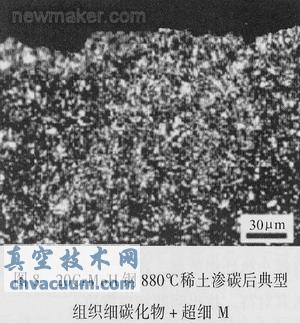
另外要解決黑色組織與表面硬度低下的問題。眾所周知,碳氮共滲是一種具有很多優(yōu)點的工藝,因為有嚴重的黑色組織而沒有被廣泛使用。其實滲碳也存在黑色組織的問題,由于黑色組織伴生有非馬氏體組織,從而使表面硬度大幅下降,使?jié)B碳層硬度分布曲線普遍存在低頭現(xiàn)象,導致齒輪早期磨損,這已是存在多年的難題。
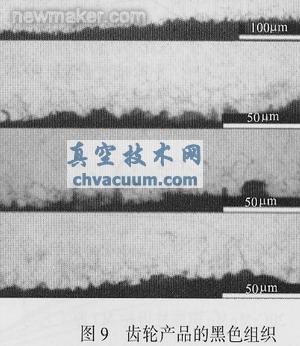
圖9是與外商配套的滲碳齒輪的黑色組織,因黑色組織閑擾尋求解決辦法,由圖9可見黑色組織相當嚴重,將試塊截面經拋光后極輕腐蝕,即清晰可見表層有大量黑色網絡存在。這種網絡叫做黑網,主要由合金元素Cr被氧化析出,基體變?yōu)榉邱R氏體,導致硬度大幅度下降。其黑網深度約在30~40μm。
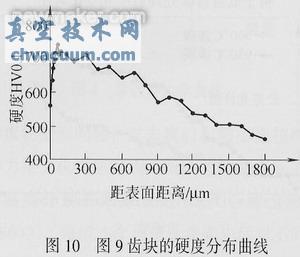
其硬度分布曲線如圖10所示。表面硬度僅550HV,嚴重影響齒輪產品的品質。研究認為黑色組織的機理是一種內氧化現(xiàn)象;氧原子沿晶界擴散,將晶界周圍的Cr原子氧化沉淀在晶界,由于基體貧Cr在油冷時轉變?yōu)榉邱R氏體,從而成為黑色網絡。根據這一形成機理,稀土滲碳時由于稀土優(yōu)先在工件表面富集并擇優(yōu)沿鋼的晶界擴散,由于與氧的親合力遠比Cr原子高得多,它將優(yōu)先與氧結合,阻礙氧原子繼續(xù)向內擴散,從而有助于減輕黑色組織。
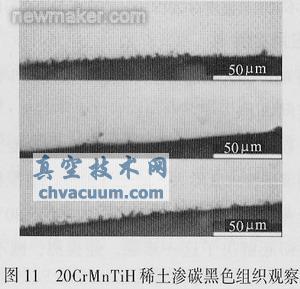
為此我們對稀土滲碳試樣進行了多次檢驗。由于晶界上也優(yōu)先沉淀析出碳化物,輕腐蝕時極易出現(xiàn)更嚴重的黑網,因而只能挑選沒有碳化物析出的試樣,用極輕的腐蝕進行檢驗,結果如圖11所示,黑色組織甚為輕微,黑網只能在個別地方隱約可見。硬度分布曲線見圖12,表層有所下降接近59~60HRC,而有碳化物析出的試樣表面硬度則高達820HV,約63~64HRC(見圖12)。由此可見,滲碳中加入足夠的稀土將是解決常規(guī)滲碳黑色組織的最簡便有效的方法。
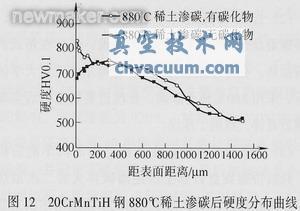
對生產現(xiàn)場實際情況各項技術的經濟指標進行對比總結如下:對汽車變速箱齒輪模數M5~M8,我們推薦采用880℃稀土滲碳,無論是滲碳速度或生產周期、能耗、齒輪熱后畸變、黑色組織、表面硬度和滲層金相組織與控制,以及降低成本、提高產品質量等方面均較原工藝920℃滲碳有著無可比擬的優(yōu)勢,尤其是減少齒輪畸變與防止熱后精度大幅下降方面的作用更為顯著。在生產出口變速箱與外商配套方面,找到了一種簡便、實效和具有中國特色的先進工藝方法。
3.載重車后橋終端螺旋盤齒與錐齒輪傳動的專用稀土滲碳工藝
(1)本傳動齒輪的工作條件及破壞形式 這是汽車齒輪中受力最復雜及工作條件最惡劣的一對傳動。當汽車急轉彎和道路崎嶇不平及凸凹反差大時,除受正常的滾動摩擦外還受動態(tài)的沖擊與高接觸應力下的滑動摩擦。若齒輪因熱處理產生變形,齒面嚙合較差或因裝配不當發(fā)生偏載還會產生局部應力集中,當這些不利因素在某種特定的條件下相互疊加將造成這對齒輪的早期破損。正常跑車時承受動態(tài)的周期性的滾動與滑動摩擦,承受極高磨擦磨損與疲勞粘著磨損,當啟動與剎車、突然加速與停車、轉彎或道路崎嶇時還要承受沖擊與多種疲勞磨損。尤其我國運輸車輛超載嚴重及鄉(xiāng)間道路路況較差,因此這對傳動的壽命很低,跑車歷程很短,成為車主頭痛之事。
根據在制造企業(yè)的了解,這對傳動齒輪的破壞形式為:①斷齒尤以錐齒較多,斷口分析其原因有嚴重超載與偏載,斷口夾雜,斷口呈粗晶狀在掃描電鏡下觀察為一標準沿晶斷口,具有氫脆斷口特征。②疲勞剝落,其形貌有點蝕、較深的塊狀剝落、局部大片疲勞剝落等。③典型嚴重磨損與疲勞磨損,嚴重磨損加疲勞剝落等等。根據其受力與破損特征,其主要原因為摩擦、粘著與疲勞裂紋的萌生與擴展,或兩者的復合。
(2)研究對策根據理論分析與實踐證明,稀土滲碳的典型標準金相組織對上述的破壞特性具有很高的抗力。眾所周知,碳化物具有很高的硬度、耐磨性及抗粘著磨損,而馬氏體晶粒及殘留奧氏體的超細化可使馬氏體的強度與韌性特別是抗斷裂的性能得到較大提高,其裂紋萌生與擴展抗力同步提高。稀土滲碳的典型標準組織(見圖13)在滲碳外表面過共析區(qū)沉淀析出細小彌散顆粒狀碳化物,其基體為超細隱晶馬氏體與殘留奧氏體,把兩者的特性合理地結合復合在一起,從而使這種組織具有很高的耐磨性(包括抗粘著)與接觸疲勞性能,能使齒輪的耐磨性及接觸疲勞壽命與彎曲疲勞壽命均同步大幅提高。因而這是提高這類齒輪齒面承載能力與延長使用壽命既簡單又有成效的方法。
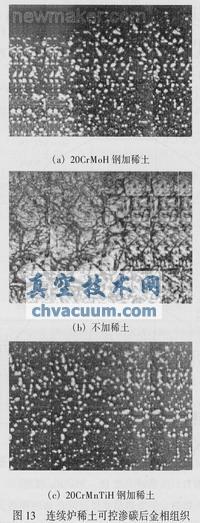
(3)中大模數齒輪的稀土滲碳工藝 即上述這對齒輪副的應用實例,滲層要求1.7~2.2mm,主動錐齒輪稀土滲碳后可直接淬火,而被動盤齒出爐后必須在淬火壓床上壓淬。滲碳可在多種滲碳爐中進行,產量很大時常在貫通式連續(xù)式滲碳爐中進行。我們曾于原哈爾濱拖拉機配件廠合作進行過稀土可控滲碳,并用于生產。實踐證明,只要工藝參數凋整得當,即能獲得較快的滲速又能獲得典型的標準金相組織(見圖13)。
(4)生產應用效果 該廠主要生產8~10t載重汽車的后橋螺旋錐齒輪副與汽車總裝廠配套,月產約2000套。用戶反饋信息為:不加稀土的金相組織符合汽車拖拉機齒輪金相檢驗標準,退貨率約為5%~7%,而加稀土可控滲碳后退貨率下降至1%~2%。證明采用稀土可控滲碳后取得了明顯的技術經濟效益。
五、結語
(1)最近研制成功的有機稀土目前尚處于試用階段,初步應用結果表明使用效果與稀土鹽相當,但可溶解性優(yōu)于前者,可在多種油溶性滲碳介質中溶人,而且不易產生堵塞,使用簡便,價格合理。并由專業(yè)化公司獨家進行生產,從而保證了產品質量與及時供應。
(2)總結過去經驗與近期試驗。根據當前我國汽車行業(yè)實際情況,特向同行推薦了具有輿型意義的兩種稀土滲碳工藝:
其一,汽車變速箱齒輪880_℃稀土可控滲碳,目標在于減少齒輪熱后產生畸變,保持較高的精度等級,為出口配套尋找具有良好綜合技術經濟指標的先進工藝方法。
其二,后橋末端圓錐螺旋傳動副,為這種以壽命很低的齒輪副提供對策。稀土滲碳典型微觀組織正好符合其受力條件與工作條件,實踐證明也產生了預期效果。
(3)稀土共滲技術是我國的發(fā)明專利,在化學熱處理與表面處理中有著其特殊的作用,其潛在特性遠未發(fā)揮,未加以充分利用,作為發(fā)明單位自感十分遺憾。稀土在上述領域有著廣大發(fā)展空間與技術市場,希望有興趣企業(yè)界共同合作,充分利用我國寶貴資源為社會創(chuàng)造財富,創(chuàng)制新的工藝技術。
(4)堅持走市場化道路,共同開發(fā)稀土滲碳、稀土滲氮、稀土多元共滲以及稀土表面處理等市場。按市場需求共同開發(fā)新的產品,新的工藝技術,繼續(xù)走創(chuàng)新之路。